Table of Contents
Industrial Freeze Drying: From Vaccine Production to GMO Seeds
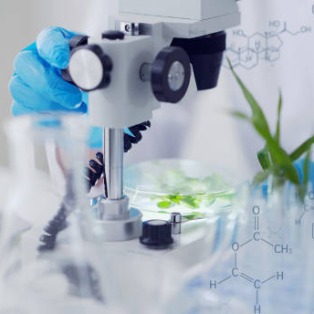
Industrial freeze drying, or lyophilization, is a transformative technology bridging biotech and agriculture. By removing moisture under controlled conditions, it preserves the integrity and functionality of sensitive materials, from life-saving vaccines to genetically modified seeds. This article explores cutting-edge applications, equipment specifications, and the pivotal role of freeze drying in modern science.
Cutting-Edge Applications of Industrial Freeze Drying
mRNA Vaccine Stabilization
The COVID-19 pandemic underscored the importance of stabilizing mRNA vaccines. Freeze drying plays a critical role by:
Removing Water: Converts liquid formulations into stable powders, eliminating the need for ultra-cold storage (-70°C).
Preserving Lipid Nanoparticles: Protects the fragile mRNA structure within lipid carriers, ensuring efficacy during global distribution.
Extending Shelf Life: Lyophilized vaccines (e.g., Pfizer’s COVID-19 booster) can be stored at 2–8°C for months, enhancing accessibility in remote regions.
Case Study: Moderna utilizes lyophilization to develop thermostable mRNA vaccines for diseases like Zika and HIV, aiming to simplify logistics in low-resource areas.
Soil Microbiome Preservation
Freeze drying revolutionizes sustainable agriculture by preserving beneficial soil microbes:
Long-Term Viability: Microbial inoculants (e.g., Rhizobia bacteria) remain viable for 5+ years, promoting nitrogen fixation in crops.
Bioremediation: Lyophilized cultures of pollutant-degrading microbes (e.g., Pseudomonas) are deployed to clean oil spills and heavy metals.
Seed Coating: Freeze-dried fungi like mycorrhizae enhance seed germination and drought resistance.
Agricultural Impact: Companies like Bayer AG use lyophilized microbes to reduce chemical fertilizer reliance, aligning with regenerative farming practices.
Equipment Specifications for Industrial-Scale Freeze Dryers
Key Components
Vacuum Chamber: Maintains low pressure (0.01–0.03 mBar) to enable sublimation.
Condenser: Cools to -80°C to trap vaporized moisture.
Temperature-Controlled Shelves: Adjust from -50°C (freezing) to +30°C (secondary drying).
Refrigeration System: Uses eco-friendly refrigerants like CO₂ or ammonia for large-scale operations.
Industrial vs. Laboratory Models
Feature | Industrial Freeze Dryers | Lab-Scale Units |
---|---|---|
Capacity | 300–3,000 kg per batch | 1–10 kg per batch |
Automation | Fully programmable (PLC systems) | Semi-automatic controls |
Energy Use | 30–120 kW per batch | 2–5 kW per batch |
Applications | Vaccines, bulk seeds, bioremediation | Research samples, small batches |
Innovation Spotlight: Advanced freeze dryers now integrate IoT for real-time monitoring of pressure, temperature, and moisture levels.
Bioremediation Cultures Storage
Freeze drying offers a robust solution for preserving microbial consortia used in environmental cleanup:
Pollutant-Specific Strains: Cultures like Deinococcus radiodurans (radiation-resistant) are lyophilized for nuclear waste remediation.
Rapid Deployment: Rehydrate and activate cultures on-site for oil spill treatment.
Stability: Maintain metabolic activity for years without cold chain dependency.
Example: BioSphere Solutions markets freeze-dried Bacillus subtilis for degrading pesticides in contaminated soils.
The Pharmaceutical Freeze Drying Process
Formulation: Active ingredients (e.g., mRNA, proteins) are mixed with stabilizers (sucrose, trehalose).
Freezing: Rapid cooling to -50°C to form ice crystals.
Primary Drying: Sublimation under vacuum removes 95% moisture.
Secondary Drying: Residual moisture (<1%) is desorbed via gentle heating.
Regulatory Compliance: Adheres to FDA and EMA guidelines for sterility and reproducibility.
Future Trends in Lyophilization
Energy Efficiency: Solar-powered freeze dryers for off-grid agricultural communities.
AI Optimization: Machine learning algorithms predict optimal drying cycles.
3D-Printed Vaccines: Lyophilized mRNA formulations for customizable drug delivery.
Conclusion
Industrial freeze drying is a cornerstone of biotech and agricultural innovation. From stabilizing groundbreaking mRNA vaccines to preserving the microbial allies of sustainable farming, this technology addresses global challenges with precision. As advancements in automation and sustainability emerge, lyophilization will continue to unlock new frontiers in science and industry.